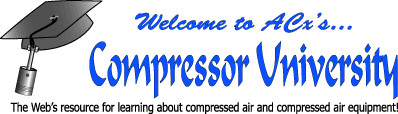
If you are here, it is because you have a question about compressed air. This page has some of the basics to get you started as part of the FAQ section. Many questions can be answered there but if you want more in-depth information, please click the appropriate button at the left. You will be taken to a page dealing with that specific topic. If you still don’t find an answer to your question please click here and you can ask us directly.
Some Commonly Asked Questions about Compressed Air:
|
Answers:
- What’s with all the different types of compressors? Which is best for me?
Answer: There are four major types of compressors; rotary screw, reciprocating, rotary vane and centrifugal. These comprise 99% of industrial compressors. As far as which is best for you, it really depends on how you intend to use it. This is a case where we suggest you call us (419-661-9568) or email us info@aircompressorexchange.com. We will go through a list of questions that will help us determine which is best in your application. We don’t publish the list because sometimes it isn’t all that easy and it requires some thought. The last thing we want to do is send you, however unwittingly in the wrong direction.
- Why do my tools/equipment have water dripping from them even though I have an air dryer?
Answer: There can be a couple of answers to this. First, is your dryer doing its job? In other words, did it used to dry the air and now it doesn’t? If it’s a refrigerant dryer, you may have a leak in the refrigerant. If you have a desiccant dryer, your desiccant may be old or contaminated. Beyond this, either type could have a control malfunction. The other issue arises in the plant where the air never quite dries out. Some days may be better than others but it’s never good and dry. Chances are, in this case you either have a dryer that is too small (common if you have added a trim compressor) or that you have a line somewhere in the plant that goes outside the building where it is subject to the ambient air. If you have a refrigerant dryer, it simply cannot cope with low temps and/or extremes in humidity. A desiccant dryer is called for even though they are far more expensive. The reason stems from the fact that the refrigerant dryer has a dew point of approximately 35 degrees F whereas a desiccant dryer’s dew point is down around -40 degrees F. Simply put, when properly sized, the desiccant dryer does a much better job at drying the air. For the normal plant, this difference isn’t noticeable. It is when you get to the extremes that the problems become apparent.
- Will water hurt my air supply?
Answer: Absolutely! Water corrodes pipes, valves, machinery controls. None of this is good. When controls malfunction, production can be hurt and this, once again costs money.
- What is a receiver? How big does it have to be?
Answer: A receiver is a tank attached to the air system that stores compressed air. It does this to even out any brief high demands on the system. In other words, it keeps the pressure more constant. A common misconception is how long it will help. In most systems, this time is measured in seconds. If you find your system pressure dropping periodically, don’t blame the receiver. Look for another cause such as the compressor itself (it may be too small) or maybe the system piping is too small. This latter problem is more common than you think. So how big to make the receiver? Usually, four times the volume of your compressor in CFM is a good starting point. In other words, if your compressor produces 100 CFM of air, them you should have a receiver of about 700 gallons or so.
- Do I need an air dryer?
Answer: Under most circumstances, yes. In an air system, water = corrosion, pure and simple. Portable air compressors typically don’t have dryers but they use tools designed for wet air. Not so in a plant’s environment. Pneumatic controls are very sensitive to corrosion caused by wet air. Valves become sticky with wet air. Pneumatic cylinders can cease to function when they begin accumulating water (or ice) within the cylinder’s body. What is more expensive, a properly sized dryer or constant maintenance?
- Which type of air dryer do I need?
Answer: This isn’t a simple question but to get you started, please click here
- How big of an air compressor do I need?
Answer: Proper compressor sizing is a subject that could fill a book! To get you started though, there are some simple considerations.
- Add all the current uses of air in your facility in CFM. This will give you the minimum size required. Add 25 % or so to allow the compressor time to rest (load/unload cycling)
- Break the preceding down by shift (if applicable). If ther is a wide disparity of need shift to shift, you may want to have 2 compressors in the system. One functions as the main compressor and the other provides “trim” air for the larger shift. This will save considerable money over the years. Alternatively, you may want a variable speed compressor
- Decide on your company’s expected growth over a reasonable period of time. Decide if these growth plans involve more air. If so, you may want a variable speed compressor
- Decide if you need a backup plan. Can you function temporarily if the air supply goes down? If not you actually need two systems. In practice, we suggest you alternate their use.
This should give you enough information to get you started. As
you can see there are a lot of variables to take into consideration. Please
DON’T be tempted to buy a couple of small compressors thinking
you can buy more and more of them as the need arises. We
recently went into a plant that had 5 compressors running. There
was no master control system and as a result, the compressors fought
each other to the tune of over $30,000 a year in wasted air!
- Why can’t I just get a really big air compressor and never worry if I have enough air?
Answer: Absolutely, you can! I’ll be happy to sell it to you except that you probably won’t be in business a few years down the road. Even unloaded, a compressor consumes significant energy. This means that you will be paying to run a motor that does nothing. Proper sizing is not an attempt to keep selling you compressors again and again. Sizing is taking all factors into account in the hope that we can strike a balance between cost and need. Generally speaking, you will spend far more on electricity to run the compressor than on the compressor itself in just a very few years. More than once, we have seen slightly used compressors on the market that companies are selling because they realized that they grossly overstated their actual air needs. When they see the electricity bills they quickly realize that it is cheaper to sell the over-large compressor at a great loss and purchase a properly sized machine. The payback is quite short.
- What is an air survey? Do I need one?
Answer: An air survey examines many of the topics in this FAQ section. In addition a full air audit may measure air volumes on a plant-wide basis as well as per machine. They generally look for and tag air leaks. We also look for wasteful uses of air such as open blows. If you think you might need an air audit, contact us. We can discuss you situation and advise you on further action.
- What’s the cheapest compressor to operate?
Answer: There is no single answer to this
question. Some air compressors are more efficient but they can
cost more in the long run to operate. Read everything you can
within this FAQ section and elsewhere in “Compressors 101”. Most
of your questions should be answered. If not contact us with
your questions. We will be happy to help.
- Aren’t four small compressors better than one big one?
Answer: It depends. If all 4 are operated simultaneously without a master control system, probably not. Air compressors all want to be top dog. They want to produce air. With too many compressors on line, they give each other false readings and they tend to actually produce LESS air than they are capable of. For multiple compressors to work together a control system must be used.
- I have one compressor but my 3rd shift uses half the air of the 1st and 2nd shifts. How can I save money here?
Answer: This can be accomplished a couple of ways. Using two compressors is one way. One compressor handles the main load and the other is used in a “trim” capacity. The other way is a single variable speed compressor. This compressor has the ability to “throttle back” and produce only what air is needed. At least one company, CompAir, has a variable speed unit that can throttle back to 20 % or rated capacity.
|